2023 Italy Boxed Sets
10.30.2023
17×22” piezography prints initially made from a 2000 trip to Italy left me feeling they could be “more”, over the years. They are nice, I showed them, sold a few, and over time interest faded in the fog of ongoing newer work. Small old world architectural etchings in an Italian deli brought them back to mind, illustrating that these don’t need size and could have a spirit more suited to the work. Coincidentally I found a beautiful small sheet handmade Japanese paper from Hiromi and started working with how it took ink. This work looked wonderful on it.
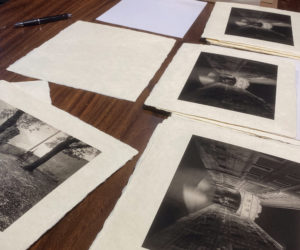
printing and printing
The result is four boxed sets of sixteen selected from the initial larger group of twenty-six. I’m concentrating here on the steps taken to make the custom boxed sets and the decisions along the way, hoping this may be helpful. Custom case production and the Letterpress printing have to be subbed out, before getting too carried away I contacted Ed Marquand at Paper Hammer and Daymoon Press to secure their services and get input before making too many decisions. The print size predetermined by my paper choice, sixteen work/reject prints on the paper went to Ed so they could determine case size, that in turn allowed label, title page, and colophon design.
Simple for a custom portfolio, a clamshell box. Additional elements are title sheet, print interleaves, and a colophon. Required decisions for design and practicality are- case cover cloth, case lining material, label material, letterpress paper and interleave material, font choice and text design. Paper Hammer, being a custom box maker and more, had beautiful materials on hand, sent me samples and swatches of many options, I also ordered samples from a few other suppliers.

selecting from samples for case cover cloth, lining material, letterpress stock
I chose the actual photo print paper for the label which Day Moon Press trimmed to size and completed the printing as I watched, fascinated. They were sent to Ed, with my decisions for outer cloth which he stocked, and inner lining material I had ordered from Hiromi, box construction could begin. They trimmed out sheets from their stock of the letterpress paper I selected and sent to Day Moon Press, who had my final text/type design for printing. The interconnected tasks of all involved must be considered and planned, in the meantime at home I completed the actual prints. Paper Hammer also cut a large supply of the chosen interleave to size, which I received from them with the completed cases over in beautiful Tieton WA..
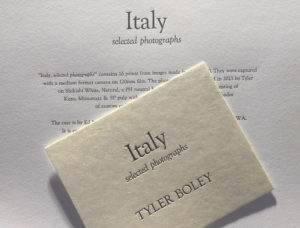
Day Moon Press’s beautiful work
Final prints completed and inspected, each had to be signed, numbered, and negative number, dates, etc. put on the back. My increasing dysgraphia became immediately apparent. A high percentage are barely legible. That added to the imperfections of the handmade paper- I’ve chosen to call “charming”.

hand cramps
All that was left was to assemble all the completed parts into the four full boxed sets. The input and mastery of Tess at Daymoon Press, Ed Marquand and Maria Solorio at Paper Hammer Studios contributed mightily to this project. Input from Monika Chwojko, Lauren Henkin, and Jeff Corwin was also essential.
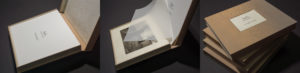
showing off Paper Hammer’s work
All of the materials and people involved are in the colophon, pasted below-
“Italy, selected photographs” contains 16 prints from images made in Italy, 2000. They were captured with a medium format camera on 120mm film. The photographs were printed in 2023 by Tyler on Fuji Shikishi White, Natural, a PH neutral handmade Japanese paper consisting of Kozo, Mitsumata & SP pulp with no optical brighteners, using seven shades of custom carbon monochromatic pigment inks.
The case is by Ed Marquand and Maria Solorio at Paper Hammer Studios, Tieton, WA. It is covered with Iridescent Orange Japanese Ginga Bookcloth; lining paper is Amate Solid Natural, made in Mexico using the bark from the Jonote tree.
The title page, and colophon were letterpress printed on Stonehenge White Cover, handset in Goudy Old Style, at Day Moon Press, Seattle WA.
Individual prints are protected by Neenah UV/Ultra interleaves.
The four boxed sets were printed, crafted and completed in 2023.
Links
Piezography- https://shop.inkjetmall.com https://piezography.com
Hiromi- https://hiromipaper.com
Day Moon Press- http://daymoonpress.com
Paper Hammer- https://www.paper-hammer.com
Monika Chwojko- @vintage_vis, @visionofforest
Lauren Henkin- https://www.laurenhenkin.com https://www.thehumane.space
Jeff Corwin- https://www.jeffcorwinfineart.com
Hi Tyler,
I am a photographer / printmaker working in historical processes, primarily Pt/Pd and polymer gravure. I have been using piezography since about 2008/2009 (I assisted Jon Con a few times when he taught in Santa Fe). I am currently printing with Pro inks on a P-6000.
Recently I have started exploring printing piezography on uncoated paper. And in admiring your work for sometime now you have also gone done that rabbit hole, a few times, :-).
I am writing to see if you would share your workflow experiences here. I have used the Piezography Professional Tools (PPETv2.2). As you probably know that is an ink limiting function as part of the tools but it is not documented very well.
I am currently testing HFA Sumi-e and have printed the Spyder 129 step chart using the Uncoated-Master starter .quads (at 100% ink). I have also printed these same starter curves using 50% and 75% less ink.
I have also noted that when I initially printed a test image at 100% ink the paper “rippled”. I believe that ink in the dark areas was being absorbed into the paper causing the paper fibers to shrink differently, hense the ripples; and in the darkest areas of the print you can see, when looking sideways onto the print, a dark “band”. At that point I knew I probably needed to limit the ink.
In reading through the inkjetmallforum blog on this topic (there are only a few references to printing on uncoated paper) the notable one was posted by Walker where he says to limit first and then lineariize. But there are no instructions or hints on how much to limit and once the targets are printed how to evaluate them to determine the “right” amount of limiting to prevent the “rippling” and “banding”. Certainly I can evaluate the backside of the test images and look at the darkest squares and see if there is any “pooling”, i.e., where the paper is no longer perfectly flat due to the ink load. I have also plotted these.
I should also note that dmax, in an absolute way, is not that important to me. I am sure I will be able to achieve a “believable” black. The contrast of the image may have to be adjusted but that is a straightforward change. It is certainly the case when comparing these flawed work prints on Sumi-e with coated paper (e.g. HFA Bamboo) the uncoated paper has more life to it: the image seems to be in the paper as opposed to sitting on top (similar qualities to my Pd. prints).
I will stop here. Please let me know if you have any questions. And any helpful hints would be most appreciated.
Hello Michael, thank you for your interest. Unfortunately my working/tweaking knowledge of QTR is extremely limited. I use the Ergosoft RIP, and have for decades now. I honestly wouldn’t know where to begin perfecting individual limiting, underink levels, total ink, etc. in QTR. FWIW a little of using Studioprint for this stuff is addressed here- https://tylerboley.com/uncoated-fine-art-papers-and-ink-conclusions-and-results/
But I can’t imagine how this may help you. Regarding ink absorption resulting in ripplling, I was only willing to limit for bleed or mottle, Walker told me about reverse rolling prints to undo rippling, which I took to an extreme and describe here about half way down- https://tylerboley.com/about-the-cloudscapes/
I wish you the best with your efforts, I think this is a viable way to go, with good reason to pursue it. I’m sure this is possible with QTR, it offers control, one way or another, of each ink, I just don’t know how. I can at least confirm that one would linearize last, after the ink setup has been finalized. There is a pewizography FB page, where the usual suspects post sometimes, would be worth asking there- https://www.facebook.com/groups/884976836142463